La caratterizzazione meccanica dei materiali è una fase di studio e analisi importantissima, soprattutto quando ci si muove nell’ambito dell’Additive Manufacturing.
di Enrica Riva, Università di Parma
La sfida della fatica nei materiali additivi
Negli ultimi anni, la fabbricazione additiva (AM) ha guadagnato terreno in molteplici settori industriali, dall’aerospaziale al biomedicale, grazie alla possibilità di realizzare componenti metallici estremamente complessi e alleggeriti. In particolare, la tecnologia Powder Bed Fusion (PBF) consente di produrre pezzi ad alte prestazioni, rispondendo a esigenze di design avanzato e di riduzione dei tempi di consegna. Tuttavia, l’impiego di materiali PBF in ambito strutturale impone una valutazione accurata delle proprietà meccaniche, in particolare della resistenza a fatica, anche considerando i necessari post-trattamenti e la determinazione del miglioramento dele proprietà meccaniche che sono in grado di indurre.
La fatica è il fenomeno per cui un componente, sollecitato da carichi ripetuti per un numero di cicli molto elevato, giunge a rottura in maniera spesso imprevedibile. Considerato che oltre l’80% dei guasti in campo meccanico è associato a meccanismi di fatica, appare piuttosto evidente quanto sia cruciale la disponibilità di dati sperimentali affidabili, cui i progettisti possono fare riferimento. Nel caso di materiali prodotti mediante AM, la situazione è resa più complessa dalla presenza di difetti interni, dall’anisotropia microstrutturale, dalla rugosità superficiale tipica della produzione strato su strato e, non da ultimo, dalla numerosità e influenza dei parametri di stampaggio.
I metodi di caratterizzazione a fatica tradizionali, normati da standard come ASTM E466 (prove di fatica assiale) o ISO 1143 (prove di fatica in rotazione), prevedono l’impiego di provini di dimensioni relativamente grandi (lunghezza >80 mm, diametro 5-6 mm). Ciò comporta un considerevole consumo di materiale, costi elevati e tempi di lavorazione lunghi. Inoltre, la finitura superficiale dei provini standard è spesso lavorata (lappata o rettificata) per rispettare le tolleranze richieste dalle norme: questo però altera la configurazione as-built dei componenti PBF, introducendo uno scostamento rispetto alle reali condizioni operative.
TP Engineering: dall’idea alla realizzazione di un innovativo spin-off
TP Engineering S.R.L. è uno spin-off accademico che nasce proprio con l’obiettivo di sviluppare soluzioni d’avanguardia per la caratterizzazione meccanica dei materiali.
Unendo il rigore della ricerca scientifica a una spiccata attitudine per l’innovazione, l’azienda è in grado di progettare e realizzare attrezzature su misura per il cliente, da integrare nei laboratori, nei reparti qualità o direttamente come test in linea per la qualificazione dei prodotti. Questo connubio si traduce in prodotti e metodologie che guardano alla sostenibilità, all’economicità e all’affidabilità delle prove meccaniche.
L’impegno di TP Engineering è testimoniato dalle numerose collaborazioni con enti di ricerca e università nazionali e internazionali. Tra i progetti più rilevanti, si evidenzia lo sviluppo della macchina MINI FP2, un’apparecchiatura da banco progettata per condurre prove di fatica su mini-provini mediante carico a flessione ciclica. Il successo di questa tecnologia ha portato alla vendita delle prime quattro unità della MINI FP2, adottate da istituzioni prestigiose come il Politecnico di Milano e l’Università di Pretoria in Sudafrica.
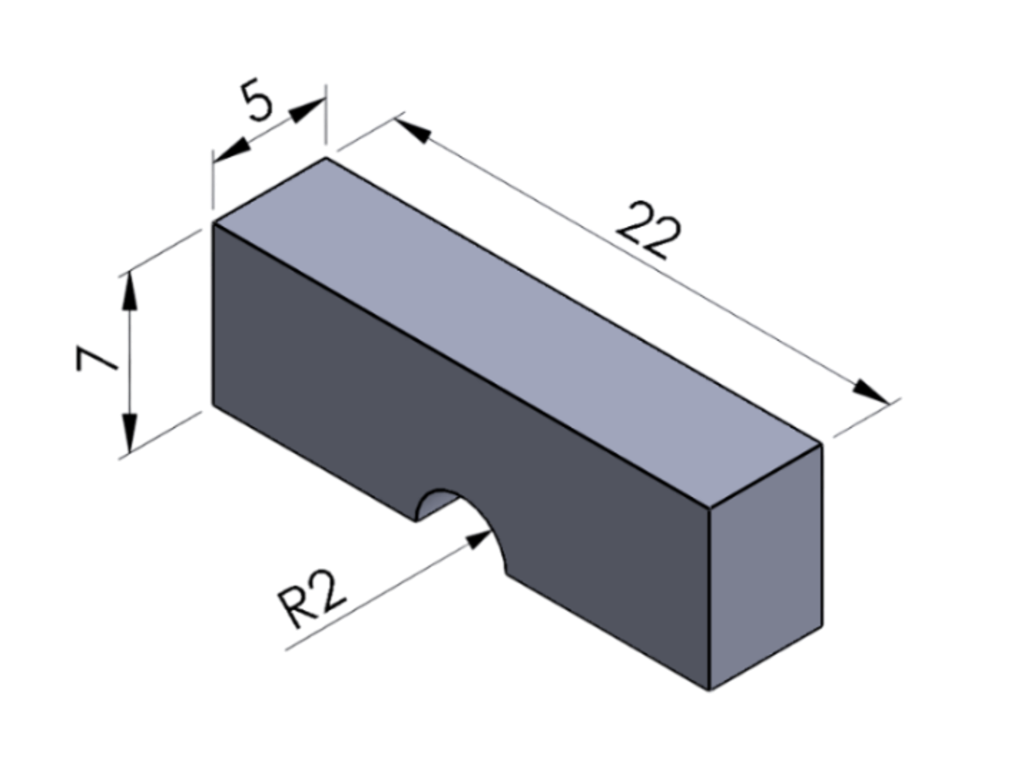
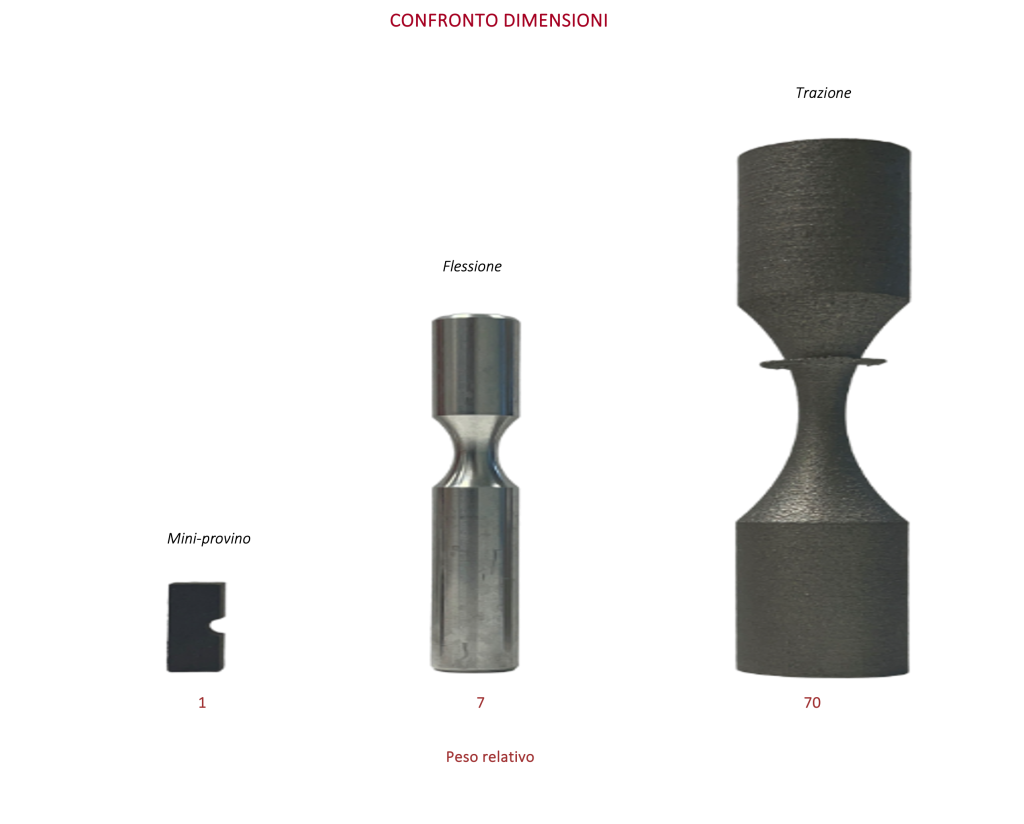
I molteplici aspetti da considerare nei test di fatica di materiali PBF
La fabbricazione additiva in generale, e la tecnologia PBF in particolare, presentano numerosi vantaggi: libertà progettuale, possibilità di realizzare geometrie complesse e riduzione degli scarti di materiale. Tuttavia, per sfruttarne appieno il potenziale in ambiti strutturali (ad esempio in componenti critici per motori aeronautici o parti sottoposte a sollecitazioni cicliche in campo automotive), è essenziale disporre di dati affidabili sulle prestazioni a fatica.
Le prove di fatica convenzionali implicano un grande dispendio di risorse, in particolare di tempo e di materiale. Basti pensare che, per costruire un set di provini standard per ottenere una singola curva S/N, è necessario un ingente quantitativo di polvere metallica (costosa e non sempre facilmente reperibile). Inoltre, le macchine di prova tradizionali (servo-idrauliche, o per flessione rotante) hanno costi di acquisto elevati, sono particolarmente energivore (una singola caratterizzazione a fatica può durare oltre un mese), richiedono manutenzione periodica e operano spesso a frequenze relativamente basse (10-20 Hz) se si considera la necessità di un controllo preciso del carico.
Altre criticità riguardano:
- Finitura superficiale: l’as-built PBF è generalmente rugoso e caratterizzato da imperfezioni superficiali che possono fungere da inneschi per cricche da fatica. Rimuoverle con lavorazioni meccaniche può migliorare le prestazioni, ma ciò non sempre rispecchia lo stato reale del pezzo in esercizio.
- Orientamento di stampa: la direzione di crescita del pezzo influenza la microstruttura e la distribuzione dei difetti, con conseguenze sulle proprietà a fatica. Spesso, i metodi di test convenzionali limitano la possibilità di studiare diversi orientamenti, poiché i provini risultano costosi e lunghi da preparare.
MINI FP2: la risposta di TP Engineering
Per ovviare a queste problematiche, TP Engineering ha sviluppato la MINI FP2, una macchina compatta e “user friendly” in grado di realizzare prove di fatica a flessione alternata su mini-provini (Figura 1). L’idea di fondo è stata quella di miniaturizzare sia il provino sia il macchinario di prova, mantenendo però una correlazione robusta con i risultati ottenuti dai test tradizionali.
In particolare, la MINI FP2:
- Riduce drasticamente il consumo di materiale, dal momento che ogni mini-provino misura circa 22 mm in lunghezza e 5×5 mm nella sezione netta. Per fare un confronto, con la stessa massa di polvere con cui si stampano 5 provini standard a trazione, è possibile produrre oltre 200 mini-provini.
- Consente di testare provini as-built, evitando lavorazioni post-produzione che falserebbero la valutazione dell’effetto della rugosità superficiale sulle prestazioni a fatica.
- Opera con un carico ciclico a flessione piana, enfatizzando il ruolo delle imperfezioni superficiali e rendendo i test particolarmente sensibili alla condizione “as built”. Nonostante le dimensioni da banco, la MINI FP2 è in grado di generare tensioni massime oltre gli 800MPa
- Integra un software dedicato (MINI FP Controller) che permette di impostare e monitorare la prova in tempo reale, con un arresto automatico al raggiungimento del run-out o in caso di rottura del provino.
- Lavora a frequenze fino a 50 Hz, con un consumo energetico inferiore a 500W grazie all’alimentazione monofase 230V. Ciò si traduce in un risparmio energetico che può raggiungere il 90% rispetto alle macchine servo-idrauliche o ai sistemi per flessione rotante di dimensioni standard, con velocità di test pari se non superiori
- Non richiede personale estremamente qualificato per un suo impiego affidabile.
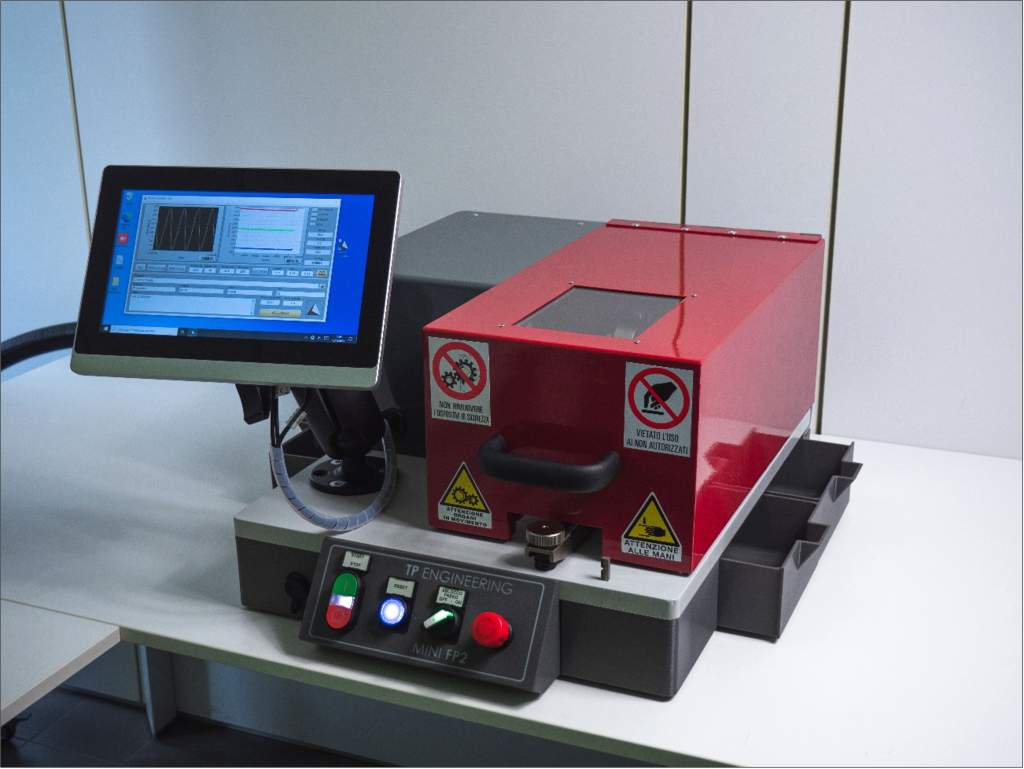
Geometria dei mini-provini e vantaggi correlati
Il disegno standard del mini-provino prevede una sezione netta 5×5 mm con un leggero intaglio centrale, necessario per concentrare le sollecitazioni in un’area definita e favorire l’innesco della cricca in una zona controllata (Figura 2). In questo modo, è possibile analizzare l’influenza della finitura superficiale e di eventuali difetti interni sulla vita a fatica.
La scelta di miniaturizzare i provini risponde all’esigenza di:
- Limitare l’uso di polvere metallica, soprattutto quando si tratta di leghe rare o costose (es. Inconel 718, leghe di titanio, superleghe a base nichel).
- Aumentare la frequenza dei test: provini più piccoli consentono carichi più ridotti e sistemi di prova più semplici, con una frequenza di test maggiore rispetto ai 10-20 Hz tipici.
- Estrarre provini anche da zone sottili di un componente reale, senza stravolgere la geometria del pezzo stampato. Questo aspetto è fondamentale quando si vuole verificare la qualità di specifiche regioni critiche.
- Studiare molteplici configurazioni (orientamento di stampa, trattamenti superficiali, trattamenti termici) in modo più rapido ed economico, grazie alla possibilità di realizzare numerosi mini-provini in un singolo job di stampa.
Validazione e confronto con i metodi tradizionali
Per dimostrare la validità della MINI FP2, TP Engineering ha condotto numerose prove di correlazione, affiancando i test con mini-provini a quelli svolti con provini standard, in conformità a norme come ASTM E466 o ISO 1143. I risultati hanno evidenziato un’ottima sovrapposizione delle curve S/N, dimostrando che la metodologia basata su mini-provini non compromette l’accuratezza del dato sperimentale. Al contrario, l’uso di provini miniaturizzati rende spesso più chiaro l’effetto della finitura superficiale e dei difetti tipici della PBF: grazie alla flessione ciclica piana, le cricche si innescano quasi sempre in prossimità della superficie, enfatizzando il ruolo di rugosità, porosità e finitura superficiali, parametri fondamentali nella resistenza a fatica di un componente.
In Figura 3, sono riportate le curve SN di una campagna sperimentale di confronto condotta su AlSi10Mg (flessione rotante provini standard vs. flessione piana mini-provini), sia allo stato as-built che lucidato.Oltre a ciò, la collaborazione con università e centri di ricerca internazionali (in Europa e Sudafrica) ha portato alla pubblicazione di articoli scientifici che hanno consolidato la validità e la robustezza del metodo. Questo patrimonio di conoscenze viene costantemente aggiornato, andando a costituire un database di dati a fatica su diverse leghe e con differenti parametri di processo.
Sostenibilità e prospettive di mercato
La MINI FP2 non rappresenta solo una soluzione tecnica efficace, ma risponde anche alle esigenze di sostenibilità e contenimento dei costi, sempre più centrali nell’industria manifatturiera. Ridurre il consumo di polvere metallica e lavorare a potenze più basse significa abbassare la carbon footprint associata ai processi di validazione meccanica. In un’epoca in cui le aziende mirano a ridurre l’impatto ambientale, questa caratteristica rende la MINI FP2 particolarmente interessante.
Sul piano economico, la possibilità di svolgere un numero elevato di prove con un numero ridotto di risorse umane e di materiale rappresenta un vantaggio competitivo notevole. Le aziende che adottano la fabbricazione additiva per componenti strutturali possono così disporre di dati a fatica accurati, testando combinazioni di materiali, processi e finiture superficiali diverse in tempi e costi ridotti.
Conclusioni
MINI FP2 è la testimonianza di come la ricerca accademica, quando incontra l’esperienza industriale e una visione orientata alla sostenibilità, possa dare vita a soluzioni di grande impatto. La macchina, sviluppata da TP Engineering, consente di effettuare prove di fatica su mini-provini in modo rapido, economico e affidabile, garantendo al contempo una correlazione diretta con le metodologie tradizionali.
In un contesto in cui la fabbricazione additiva è destinata a crescere, sia per la complessità realizzabile sia per la riduzione degli sprechi di materiale, poter disporre di uno strumento come MINI FP2 significa accelerare la qualifica di nuovi processi e materiali, contribuendo all’evoluzione del settore e supportando le imprese nel percorso verso la produzione additiva su larga scala. TP Engineering, con la sua missione di ricerca continua e attenzione all’innovazione, si propone come partner tecnico ideale per chiunque voglia esplorare le potenzialità e i vantaggi delle nuove frontiere della manifattura additiva.
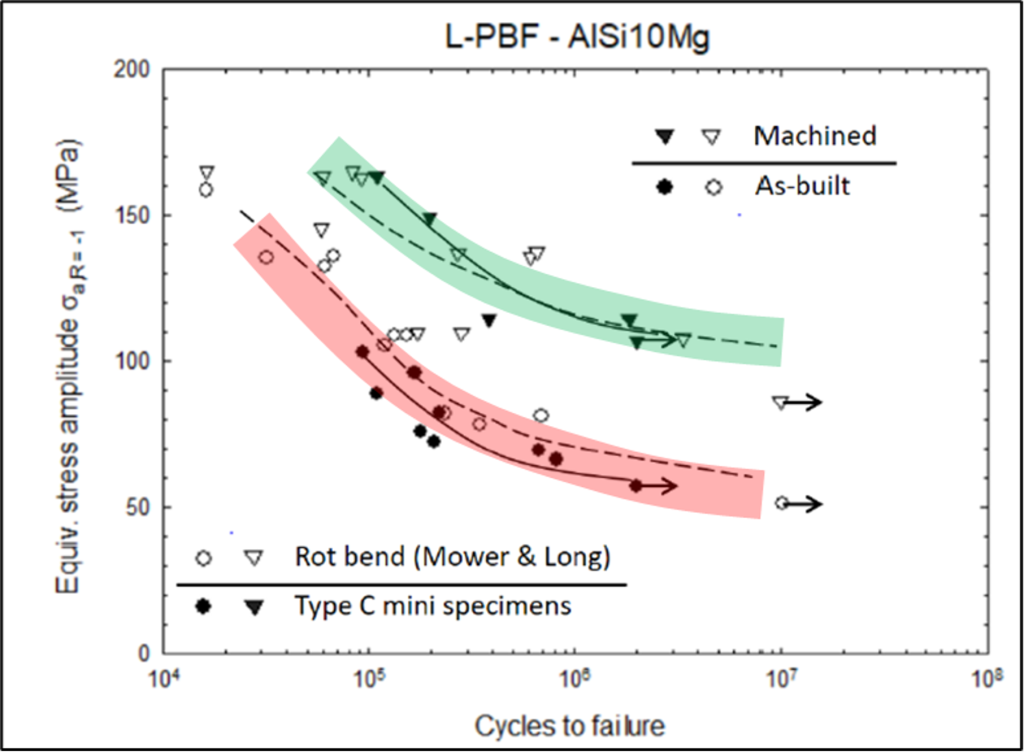