Con il passare degli anni, l’intelligenza artificiale ha gradualmente esteso il proprio raggio d’azione, affiancando alle applicazioni originarie nel campo informatico nuovi ambiti d’impiego, tra cui l’ingegneria meccanica. In particolare, si è rivelata utile in contesti dove è fondamentale ottenere risposte veloci, affidabili e facilmente ripetibili, come nelle fasi di progettazione tecnica del fattore di concentrazione delle tensioni.
di Antonio Venza, Andrea Mura – Dipartimento di Ingegneria Meccanica e Aerospaziale – Politecnico di Torino
Perché prevedere il fattore di concentrazione delle tensioni
Uno degli utilizzi più interessanti riguarda la previsione del fattore di concentrazione delle tensioni (Kt), un parametro cruciale per determinare in che modo discontinuità geometriche – ad esempio forature, intagli o variazioni di sezione – influenzino la distribuzione interna delle sollecitazioni in un componente. La possibilità di stimare correttamente questo valore consente di valutare in anticipo il comportamento meccanico del pezzo e di orientare scelte progettuali più consapevoli.
Per il calcolo di Kt, vengono comunemente adottati approcci consolidati. Gli abachi sperimentali offrono un metodo rapido, sebbene limitato a configurazioni geometriche standard. Le formule analitiche risultano utili solo in casi idealizzati, mentre le simulazioni mediante elementi finiti (FEM) garantiscono un’ottima precisione, a fronte però di una maggiore complessità modellistica e di tempi di elaborazione spesso elevati.
Quando si lavora su più varianti geometriche in fase progettuale preliminare, l’affidamento esclusivo a queste tecniche può ridurre l’efficienza operativa. Allo stesso tempo, la crescente diffusione di strumenti CAD/CAE richiede soluzioni che siano in grado di integrarsi agilmente nei moderni flussi digitali.
In questo scenario si inserisce l’approccio proposto: un modello predittivo basato su machine learning, sviluppato per stimare il valore di Kt in componenti forati – siano essi piastre o tubi – sottoposti a trazione, flessione o torsione. La costruzione e la validazione del modello si sono basate su un dataset eterogeneo, ottenuto da fonti quali abachi, simulazioni FEM e letteratura tecnica. L’obiettivo è stato quello di coniugare precisione e velocità di calcolo, offrendo al progettista uno strumento affidabile e pratico sin dalle fasi iniziali del processo progettuale.
Stato dell’arte
Quando si parla di intelligenza artificiale applicata all’ingegneria strutturale, si pensa subito a una cosa nuova, ma in realtà l’interesse per questo tema ha radici lontane. Già negli anni Ottanta si sperimentavano i primi sistemi: erano basati su regole derivate dall’esperienza tecnica e servivano soprattutto per dare supporto nella fase iniziale della progettazione. L’idea era interessante, ma in pratica non hanno mai davvero preso piede. Il motivo? Troppa distanza dalla realtà: bastava introdurre qualche incertezza nei dati o affrontare vincoli complessi per mandare tutto in crisi. Alla fine, questi strumenti finivano per essere utili solo in esercizi didattici o modelli molto semplificati.
Le cose sono cambiate davvero all’inizio degli anni Duemila. Con i computer sempre più potenti e una quantità crescente di dati a disposizione, si è aperta la strada al machine learning.
L’avvento dei metodi computazionali
Qui il salto è stato notevole: non c’era più bisogno di scrivere un modello fisico dettagliato, bastava fornire dati sufficienti perché l’algoritmo imparasse da solo le relazioni. Uno degli esempi più noti è l’uso delle reti neurali per stimare la resistenza a taglio del calcestruzzo — con risultati che, in certi casi, reggevano tranquillamente il confronto con quelli dei metodi tradizionali. Nel frattempo, anche algoritmi come Random Forest o Support Vector Machine venivano applicati per stimare proprietà meccaniche in base a geometrie o materiali, con buoni risultati anche su forme poco convenzionali.
Ma l’intelligenza artificiale non si limita a fare previsioni. Oggi gioca un ruolo importante anche nel monitoraggio delle strutture. Grazie ai dati raccolti da reti di sensori, è possibile individuare in tempo segnali di degrado, anche minimi, nel comportamento dinamico di una struttura. Questo approccio è sempre più usato nella manutenzione predittiva e permette interventi più tempestivi e mirati, riducendo i rischi.
Un altro campo che sta crescendo è quello della progettazione automatica. Alcuni algoritmi riescono a generare e analizzare tantissime varianti geometriche in tempi brevissimi, rispettando vincoli strutturali e requisiti di progetto. Se poi si affiancano a modelli fisici più classici, si possono ottenere soluzioni ibride, affidabili ma anche rapide da calcolare.
Infine, negli ultimi anni, si sta andando oltre: si usano reti neurali profonde e modelli “ensemble” anche per problemi più spinti, come prevedere la risposta sismica di una struttura o individuare micro-danni nei materiali compositi. E grazie all’evoluzione della cosiddetta explainable AI, anche questi strumenti iniziano a diventare più leggibili e trasparenti – meno “scatole nere” e più strumenti concreti, adatti a essere integrati nei processi decisionali dell’ingegneria vera.
Dataset e modello per prevedere il fattore di concentrazione delle tensioni
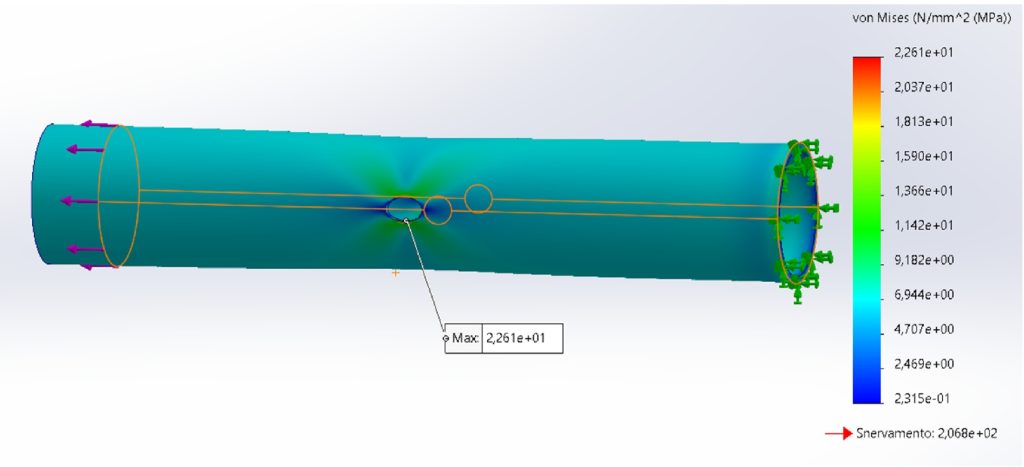
La costruzione di un modello predittivo affidabile richiede, prima di tutto, una base dati solida e rappresentativa. Per soddisfare questa esigenza, è stato predisposto un dataset ampio e ben bilanciato, in grado di coprire una varietà significativa di configurazioni geometriche e condizioni di carico. L’obiettivo principale era quello di fornire al modello un insieme informativo sufficiente a cogliere le relazioni tra la morfologia dei componenti forati e il valore del relativo fattore di concentrazione delle tensioni (Kt).
La raccolta dei dati è avvenuta a partire da tre fonti principali. I grafici, ampiamente utilizzati per stime rapide in geometrie standard, sono stati digitalizzati per ottenere una prima serie di valori attendibili. A questi si sono affiancati i risultati di simulazioni FEM, impostate in modo parametrico per includere una gamma più ampia di configurazioni non trattate nei riferimenti tradizionali. La terza componente ha incluso dati sperimentali provenienti dalla letteratura tecnica, utili a completare il quadro nei casi meno documentati o con limitata affidabilità numerica.
Per migliorare la generalizzazione e ridurre la dipendenza dalle dimensioni assolute, tutte le variabili geometriche sono state espresse in forma adimensionale. Per le piastre sono stati considerati i rapporti d/b e d/h, mentre per i tubi forati si è fatto riferimento a d/De e di/De. In questo modo, è stato possibile descrivere efficacemente le geometrie sulla base delle loro proporzioni, rendendo il modello più flessibile rispetto alle diverse scale dimensionali.
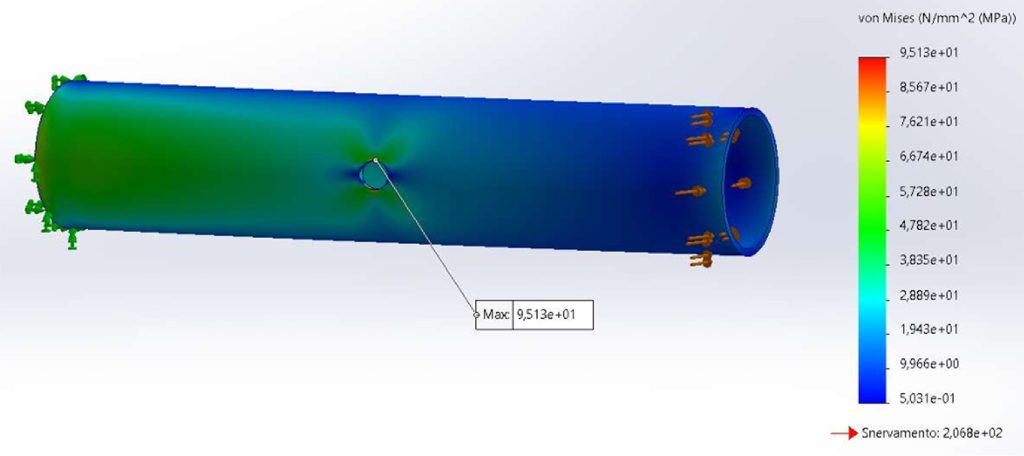
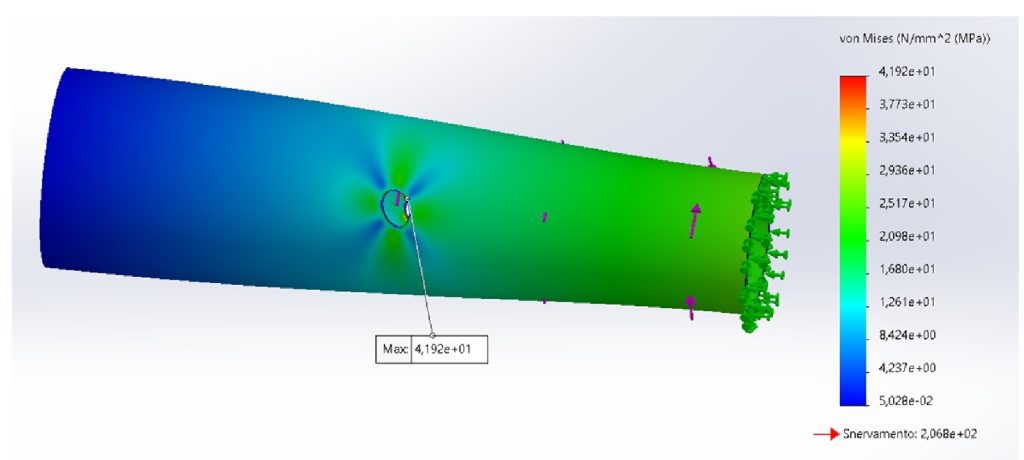
La preparazione dei dati
Una volta definito il dataset, è stata effettuata una suddivisione in due sottoinsiemi: l’80% dei dati è stato utilizzato per l’addestramento, mentre il restante 20% è stato destinato alla fase di validazione. Il modello predittivo è stato realizzato utilizzando il Random Forest Regressor, un algoritmo appartenente alla famiglia degli ensemble methods. Tale scelta è stata motivata dalla sua capacità di gestire relazioni non lineari, dalla robustezza nei confronti del rumore nei dati e dalla maggiore trasparenza rispetto a modelli più complessi, come le reti neurali profonde. Inoltre, l’algoritmo non richiede preelaborazioni onerose, né dipende da ipotesi particolarmente restrittive sulla distribuzione dei dati.
Durante il training, si è proceduto all’ottimizzazione dei principali iperparametri – come il numero di alberi, la profondità massima e la soglia minima per la suddivisione dei nodi – attraverso una ricerca a griglia (Grid Search), abbinata a una validazione incrociata. Questa procedura ha permesso di bilanciare con efficacia la precisione predittiva e la capacità di generalizzazione, garantendo prestazioni consistenti anche su configurazioni non presenti nel set di addestramento.
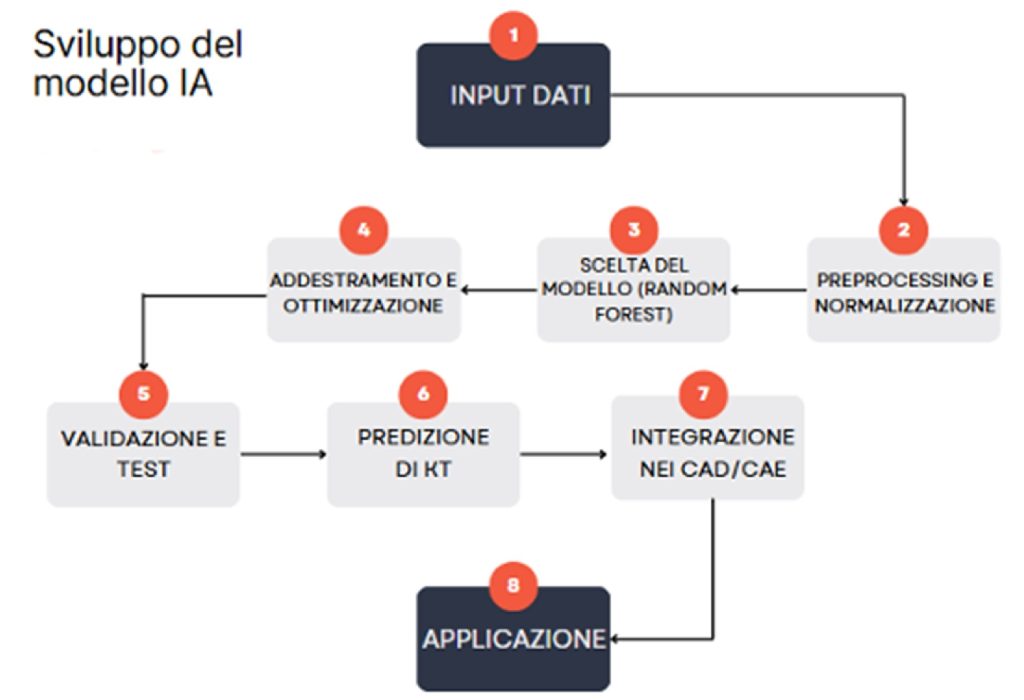
Prestazioni del modello predittivo del fattore di concentrazione delle tensioni
Per misurare l’accuratezza del modello, sono stati adottati due indicatori ampiamente riconosciuti in ambito tecnico: il coefficiente di determinazione R² e l’errore percentuale medio assoluto (MAPE). Il primo valuta la corrispondenza tra stime e dati reali, mentre il secondo fornisce un’indicazione dell’errore medio in termini percentuali. I test, condotti sull’insieme di validazione, hanno restituito risultati solidi e coerenti in tutte le condizioni di carico considerate.
Nel caso di trazione, il modello ha raggiunto un R² pari a 0,994, con un errore relativo medio del 2,7%. Per quanto riguarda la flessione, il valore è stato pari a 0,987 con un MAPE del 3,2%. Infine, sotto torsione, il coefficiente si è attestato a 0,981, con un errore medio intorno al 3,9%. Complessivamente, i valori ottenuti indicano una buona precisione anche quando i parametri geometrici subiscono variazioni contenute, segno che il modello generalizza bene anche su configurazioni non identiche a quelle viste in fase di addestramento.
Durante la validazione, si osserva un comportamento stabile anche nelle regioni limite del dominio. Il modello ha mantenuto una coerenza fisica apprezzabile, evitando salti irregolari o previsioni non plausibili. Questo comportamento suggerisce che il sistema sia riuscito a cogliere le relazioni meccaniche sottostanti, piuttosto che limitarsi a seguire l’andamento dei dati.
Per verificare ulteriormente l’affidabilità del modello, è stato effettuato un confronto diretto con due riferimenti consolidati: i grafici e le simulazioni FEM realizzate con SolidWorks. L’analisi ha riguardato tre geometrie rappresentative: una piastra con foro centrale e due tubi forati con differenti spessori. In tutte le configurazioni, la differenza tra i valori previsti e quelli di riferimento è risultata inferiore al 2%, confermando la validità del metodo adottato.
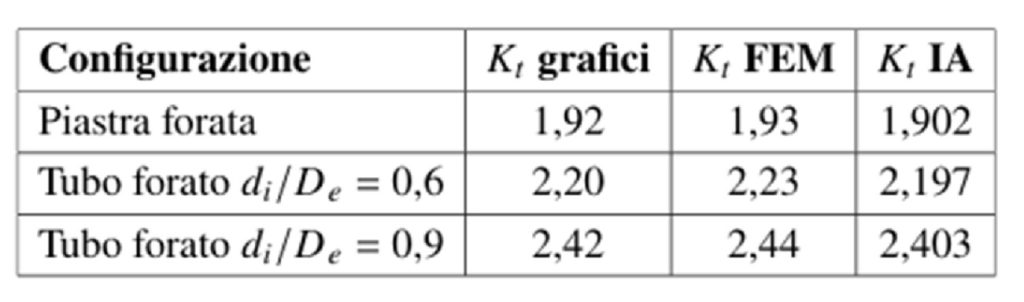
Integrazione dell’IA nei flussi digitali di progettazione
Tra gli sviluppi più concreti – e forse più sottovalutati – dell’intelligenza artificiale in ambito ingegneristico riguarda la sua integrazione nei flussi digitali di progettazione. Oggi, strumenti CAD e CAE non sono più semplici ambienti di disegno o analisi, ma piattaforme complete che accompagnano l’intero ciclo di vita del prodotto. Inserire l’IA direttamente in questi ambienti non significa solo automatizzare calcoli: vuol dire portare intelligenza strutturale all’interno del processo decisionale quotidiano.
Modelli predittivi come quello sviluppato in questo lavoro possono fornire risposte in tempo reale al progettista: ad esempio, stimare come una leggera variazione del diametro di un foro influenzi le sollecitazioni locali, o individuare geometrie meno esposte al rischio di fatica. In pratica, l’IA smette di essere uno strumento “di supporto” e diventa un collaboratore attivo nel design.
Una declinazione concreta di questo approccio è rappresentata dai cosiddetti plugin intelligenti: estensioni dei software di modellazione che sfruttano modelli già addestrati per calcolare parametri strutturali come Kt, rigidezza flessionale o instabilità locale, senza dover lanciare una simulazione FEM. Bastano pochi secondi e un semplice click. Soluzioni di questo tipo sono già in fase di test o implementazione presso centri di ricerca e aziende strutturate, con l’obiettivo di snellire i cicli progettuali e ridurre il margine d’errore nelle fasi preliminari.
Ulteriori vantaggi
I vantaggi non si limitano alla velocità. L’integrazione tra IA e ambienti CAD/CAE permette di standardizzare le valutazioni ingegneristiche, migliorare la tracciabilità dei risultati e, soprattutto, esplorare un numero molto più ampio di configurazioni geometriche. In scenari di progettazione generativa o produzione additiva, questo si traduce in una capacità maggiore di “testare” digitalmente soluzioni innovative prima ancora di arrivare al prototipo fisico.
Nel medio termine, è verosimile che questi strumenti evolvano ulteriormente grazie all’apprendimento continuo e all’intelligenza artificiale generativa. Non più solo valutazione, ma proposta attiva di geometrie ottimizzate, vincolate da requisiti strutturali e produttivi. In questo scenario, il ruolo dell’ingegnere non sparisce – cambia: da operatore che calcola, a supervisore che orienta, verifica e interpreta. E la progettazione strutturale si avvicina sempre di più a un ecosistema digitale in cui intelligenza umana e artificiale lavorano fianco a fianco.
Tempi di calcolo del fattore di concentrazione delle tensioni
Uno degli aspetti più apprezzabili di questo modello predittivo è la sua rapidità. Dove un’analisi FEM può richiedere minuti – o anche ore, se la geometria è complessa – l’algoritmo di machine learning restituisce una stima del fattore Kt in tempo reale. Questa differenza diventa determinante ogni volta che si devono effettuare molte valutazioni in sequenza, ad esempio durante analisi parametriche o cicli iterativi di progetto.
In fase di studio preliminare, è utile capire subito come cambia il valore di Kt al variare delle dimensioni di un foro o dello spessore del componente. Il modello consente di effettuare queste verifiche al volo, evitando il tempo morto tra una simulazione e l’altra. Questo lo rende particolarmente adatto anche a processi di ottimizzazione automatica, dove vengono esplorate numerose configurazioni per individuare quella più vantaggiosa in termini strutturali.
Anche nella fase di concept design il vantaggio è evidente. Quando si lavora sotto pressione, con margini di tempo ridotti ma necessità di prendere decisioni fondate, il modello rappresenta un valido supporto. Permette di orientare le scelte già nelle fasi iniziali, suggerendo se una certa soluzione geometrica ha senso da un punto di vista meccanico, senza dover attendere risultati complessi o post-processare dati FEM.
Applicazioni avanzate
In scenari più avanzati – come la produzione additiva o la progettazione generativa – la possibilità di stimare Kt in tempo reale consente di gestire con maggiore agilità anche geometrie non convenzionali. Inoltre, se il modello è integrato direttamente nei software CAD o CAE tramite plugin o API, il progettista può ottenere feedback strutturali immediati durante la modellazione, migliorando l’efficienza e riducendo il rischio di errori a valle.
Infine, in settori dove ogni pezzo è diverso dal precedente – come nella customizzazione di massa o nella progettazione su commessa – un modello veloce e affidabile può davvero fare la differenza. Permette di validare ogni nuova configurazione in pochi istanti, contribuendo a migliorare la qualità del processo, senza rallentarne i tempi.
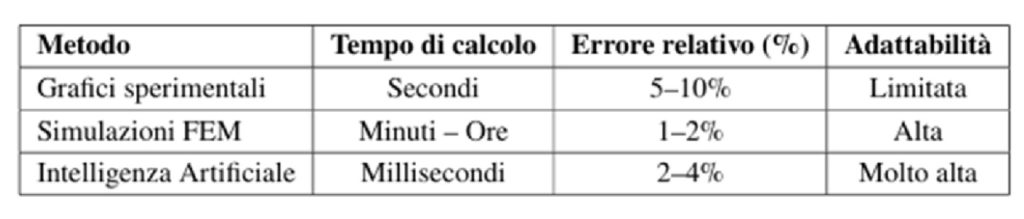
Conclusioni
Il modello predittivo presentato offre un’alternativa pratica ai metodi tradizionali impiegati per stimare il fattore di concentrazione delle tensioni in elementi forati soggetti a carichi meccanici. Il vantaggio principale emerso riguarda la rapidità nell’elaborazione dei risultati, che consente di aggirare i tempi prolungati tipici delle simulazioni numeriche.
Sebbene non miri a sostituire le analisi FEM, il modello si propone come uno strumento ausiliario utile, specialmente nelle fasi in cui è necessario eseguire confronti rapidi tra diverse geometrie. In tali condizioni, il risparmio di tempo diventa un fattore chiave, soprattutto nei cicli iterativi tipici della progettazione.
Particolarmente interessante risulta la possibilità di incorporare il modello all’interno di piattaforme CAD o CAE. In uno scenario del genere, la stima del fattore di concentrazione delle tensioni potrebbe avvenire in tempo reale, direttamente durante la modellazione. Questo contribuirebbe a ridurre l’affidamento costante su abachi o simulazioni esterne, rendendo più fluido il processo decisionale e riducendo il rischio di errore.
Nel suo insieme, il lavoro rappresenta un passo concreto verso una maggiore integrazione dell’intelligenza artificiale nell’ingegneria meccanica applicata.
Estendendo il dataset e proseguendo con la validazione, sarà possibile adattare il modello a casi più articolati, migliorando ulteriormente il collegamento tra previsione numerica e pratica progettuale.