Solitamente si considerano, per la progettazione meccanica in ambito industriale, calcoli legati al dimensionamento per prevenire il cedimento statico, il danneggiamento a fatica, le deformazioni termo-meccaniche o l’instabilità. Tuttavia, un componente può subire diversi tipi di deterioramento anche a livello superficiale, che ne compromettono la funzionalità dei quali occorre tenere conto.
di Giorgio de Pasquale ed Elena Perotti
Fra i danneggiamenti superficiali possiamo citare la corrosione, che può manifestarsi sia in ambienti atmosferici normali sia in condizioni più aggressive, come ad esempio in presenza di acqua salata. La corrosione superficiale può interagire con lo stato di sollecitazione agente sul componente, provocando effetti cumulativi più dannosi rispetto alla semplice somma dei due. Altro fenomeno di danneggiamento superficiale è rappresentato dalla cavitazione, generata dall’elevata velocità relativa tra superficie solida e particelle liquide o gassose.
Tuttavia, dal punto di vista dell’incidenza statistica, avviene molto spesso di trovare due componenti solidi sottoposti a compressione reciproca, condizione che produce tensioni di contatto le quali necessitano di particolare attenzione. Nel caso di un contatto con scorrimento relativo tra le superfici, si possono verificare diversi tipi di deterioramento, riconducibili al fenomeno dell’usura. L’esperienza dimostra che, rispetto alla rottura, il deterioramento superficiale per usura rappresenta una delle cause di guasto più frequenti nei componenti meccanici. Nonostante l’utilizzo di un lubrificante, come ad esempio olio, grasso o un film solido, possa ridurre l’intensità dell’usura, è opportuno soffermarsi sugli accorgimenti progettuali utili a contenere questo effetto e a quantificarlo.
I diversi tipi di usura
Vediamo, nel caso di contatto tra superfici solide sottoposte a pressione reciproca, come classificare il fenomeno dell’usura.
I tipi di usura più comuni sono l’usura adesiva e l’usura abrasiva; esiste poi un terzo tipo di usura detto “corrosion film wear” (letteralmente “da film di corrosione”), in cui il fenomeno che si riscontra riguarda appunto un sottile strato superficiale, che viene alternativamente rimosso dallo scorrimento fra le parti e subito dopo rigenerato. Ad esempio, questo tipo di usura si verifica tipicamente in corrispondenza delle pareti interne dei cilindri e sugli anelli dei pistoni in motori diesel alimentati con carburanti ad alto contenuto di zolfo.
Spesso viene invece confusa con fenomeni di usura un tipo di deterioramento diverso: la fatica superficiale. In questo caso, a differenza dell’usura, l’applicazione ciclica di un carico produce sollecitazioni e conseguenti cricche negli strati superficiali del materiale; queste ultime si propagano fino a causare il distacco di piccole porzioni solide e a determinare il fenomeno del pitting (originato da cricche superficiali e responsabile di cavità a superficie ridotta) o quello di spalling (causato invece da cricche sub-superficiali e responsabile del distacco di porzioni di superficie più ampia).
Tornando all’argomento di questo articolo, tutte le forme di usura sono fortemente influenzate dalla presenza di un lubrificante. In tipici componenti meccanici ben progettati, la velocità di usura iniziale sulle superfici di contatto durante il “rodaggio” può essere relativamente elevata. Man mano che le creste superficiali più pronunciate vengono ridotte ed aumenta l’area di contatto effettiva, la velocità di usura diminuisce fino a raggiungere un valore costante. Dopo un certo periodo di tempo, la velocità di usura può nuovamente aumentare a causa della contaminazione del lubrificante o dell’aumento della temperatura superficiale.
Usura adesiva
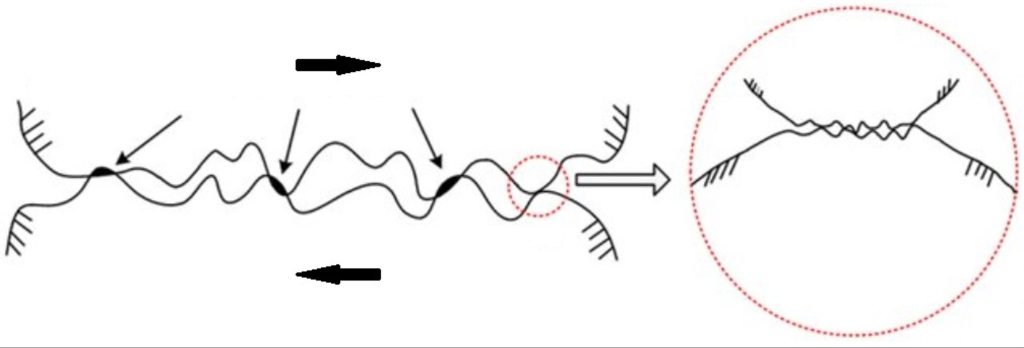
A livello microscopico, le superfici metalliche in contatto non sono mai perfettamente lisce. Nonostante la rugosità superficiale possa essere limitata a pochi micrometri, le asperità creano inevitabilmente picchi e valli, come si vede in Fig. 1. Nel momento in cui avviene il contatto con scorrimento reciproco, con pressione applicata fra le superfici, il calore prodotto dall’attrito si concentra nelle piccole aree di contatto locali indicate dalle frecce. In queste zone, le temperature e le pressioni locali raggiungono valori estremamente elevati, creando condizioni favorevoli per la saldatura fra i due materiali. Ovviamente, nonostante le temperature locali istantanee possano raggiungere il punto di fusione del metallo, l’inerzia termica del materiale circostante è molto elevata e pertanto il componente rimane freddo al tatto.
Se si verifica la fusione e la relativa saldatura delle asperità superficiali, il moto relativo fra le due parti a contatto impone che si verifichi la rottura a taglio della saldatura stessa, oppure di uno dei due materiali adiacenti. Il continuo formarsi di nuove micro-aderenze e le corrispondenti fratture danno luogo al fenomeno definito usura adesiva. Poiché l’usura adesiva è essenzialmente un fenomeno di saldatura, i metalli che tendono a saldarsi facilmente sono maggiormente soggetti a questo tipo di danneggiamento. Dopo ogni rottura locale, è frequente che si liberino piccole particelle metalliche e di ossido metallico le quali causano ulteriore usura superficiale, in questo caso per abrasione.
Il grippaggio per usura adesiva
In certe condizioni, la saldatura e l’asportazione delle asperità superficiali possono provocare un trasferimento di metallo da una superficie all’altra, con la comparsa di segni distintivi simili a graffi o solchi lineari. In certi altri casi invece, è possibile che la saldatura locale delle asperità diventi così estesa da impedire lo scorrimento reciproco delle superfici; in questo caso si può determinare il grippaggio dei componenti a contatto. Alcuni esempi fra i più noti di grippaggio sono quelli relativi ai motori, che continuano a funzionare per un certo tempo limitato dopo la perdita della lubrificazione o del raffreddamento. I pistoni possono grippare sulle pareti dei cilindri, l’albero motore può grippare sui suoi cuscinetti.
Quando due metalli simili vengono sottoposti a sfregamento con una pressione e una velocità adeguate, si creano le condizioni ideali per la saldatura delle asperità, poiché entrambe le superfici presentano la stessa temperatura di fusione. Inoltre, i legami coesivi così formati sono normalmente più forti dei legami adesivi tra asperità saldate di materiali dissimili. Per questi motivi, i metalli simili o compatibili dal punto di vista metallurgico, non dovrebbero essere utilizzati nella progettazione di parti che lavorino in condizioni di usura reciproca. In generale, maggiore è la durezza della superficie (più precisamente, maggiore è il rapporto tra durezza superficiale e modulo elastico), maggiore è la resistenza all’usura adesiva [2]
Grippaggio di un cilindro per insufficiente lubrificazione
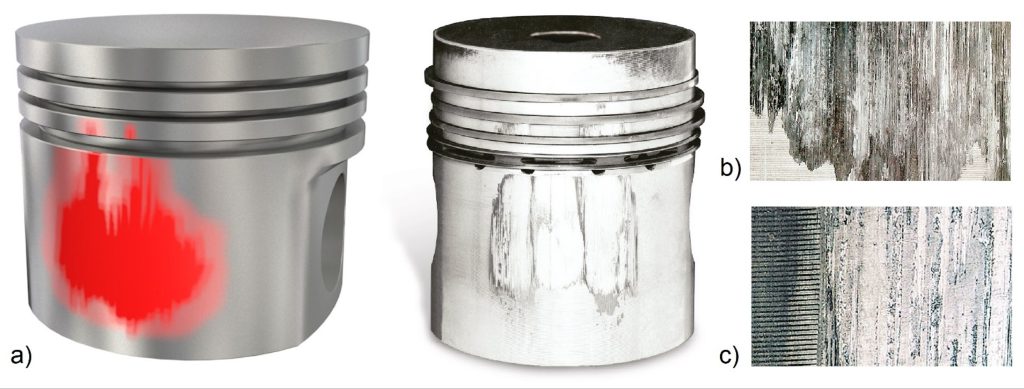
Il grippaggio dovuto alla mancanza di lubrificazione può verificarsi in generale, anche se è presente un sufficiente gioco tra cilindro e pistone. Durante questo processo, il film di lubrificante si rompe, spesso solo localmente, a causa delle alte temperature o della presenza di carburante. In queste aree, le superfici del pistone, degli anelli e della camicia cilindrica vengono a contatto senza lubrificazione, causando grave usura superficiale e grippaggio. Una situazione simile si verifica in caso di insufficiente film lubrificante tra pistone e cilindro a causa di mancanza d’olio.
Si osservano (a) segni di grippaggio sulla gonna del pistone sul lato di pressione, che in alcuni casi si estendono nella zona degli anelli. Si è verificata una grave carenza di lubrificante tra il pistone e l’alesaggio del cilindro. La superficie delle aree di grippaggio è chiara e presenta una finitura di colore simile al metallo, circostanza che indica che il film oleoso era presente ma significativamente ridotto ed insufficiente al momento del grippaggio. A causa della limitata estensione del danno, si tratta di una mancanza temporanea di olio o delle prime fasi del danneggiamento. Il danno sarebbe stato ancora più grave se il motore fosse stato utilizzato ulteriormente.
Se il film di lubrificante viene completamente distrutto, si formano aree continue di segni di grippaggio stretti, principalmente sulla gonna del pistone, che mostrano una superficie gravemente usurata e di colore scuro (b).
In caso di carenza di olio, i segni di grippaggio sono identici a quelli descritti in precedenza, a parte la decolorazione della superficie (c). La superficie delle aree di grippaggio presenta una finitura di colore simile al metallo base, senza alcuna decolorazione scura. Poiché la mancanza di olio interessa l’intera superficie del cilindro, spesso si trovano segni di grippaggio sia sul lato di pressione che su quello di anti-spinta del pistone.
Usura abrasiva
Più in generale, anche a livello pratico, ci si riferisce al fenomeno dell’usura in termini di usura abrasiva, la quale è causata dallo sfregamento di particelle su una superficie. Si tratta generalmente di particelle piccole e dure, con bordi taglienti e simili per forma granelli di sabbia, rappresentate da piccole pozioni di materiale, o di ossidi metallici, asportati da una superficie. Alcuni esempi di usura abrasiva sono la levigatura mediante carta vetrata o molatura, oppure il danneggiamento legato a lubrificante contaminato.
In generale, maggiore è la durezza di un materiale, più elevata è la sua resistenza all’usura abrasiva. La durezza delle superfici a tal fine può essere accresciuta mediante trattamenti come tempra, tempra a induzione, cementazione, nitrurazione, elettrodeposizione, rivestimento o altri metodi. Purtroppo alcuni di questi processi non sono applicabili ai componenti in qualsiasi condizione di carico e nelle applicazioni più gravose i rivestimenti induriti devono talvolta spessori elevati per garantirne la durata in servizio.
Al fine di mantenere le particelle abrasive lontane dalle superfici funzionali a contatto, è importante nella progettazione utilizzare filtri per olio e per aria, protezioni dalla polvere, tenute e altri dispositivi appropriati.
Una frequente soluzione progettuale consiste nel realizzare uno dei due componenti a contatto in materiale più morbido, in particolare quello più semplice ed economico da sostituire. Il materiale morbido, oltre ad accumulare la maggiore quantità di danneggiamento abrasivo, tenderà a inglobare le particelle presenti fra le due superfici e a proteggere il componente più pregiato. Questo criterio si adotta ad esempio nelle macchine industriali accoppiando gli alberi di trasmissione, realizzati in materiale duri e ad alte prestazioni, con boccole e bronzine morbide da sostituire periodicamente. Spesso il materiale della bronzina è così morbido da inglobare completamente le particelle abrasive ed evitare che fuoriuscendo dalla superficie agiscano come elemento di usura [2].
Fretting
Il fretting, o fretting corrosion, è classificabile come una tipologia di usura adesiva che comprende però anche elementi di usura abrasiva e di usura da film di corrosione. Si verifica quando due superfici sottoposte a pressione subiscono anche un leggero movimento relativo, come per esempio avviene fra anello interno di cuscinetto e albero, in collegamenti bullonati o rivettati, etc. Spesso il piccolo moto relativo fra le parti (dell’ordine del centesimo di millimetro) è generato dalla semplice oscillazione dei carichi esterni applicati.
Altri esempi sono le interfacce delle balestre e le pile di lamiera trasportate su lunghe distanze su rotaia o su camion. Il danneggiamento che consegue può variare dalla semplice decolorazione delle superfici, come nel caso in cui si trasportino lamiere piane impilate senza elementi di protezione fra di loro. Oppure può produrre la formazione di piccole cavità superficiali o l’asportazione di uno strato di materiale. La rugosità superficiale e la comparsa di cavità da fretting rendono la superficie più vulnerabile al cedimento per fatica. Proprio la riduzione della resistenza a fatica è la conseguenza più pericolosa del fretting.
Il meccanismo microscopico del fretting è simile a quelli già citati: il movimento causa micro-saldature fra i picchi delle superficie, con conseguenti fratture e la creazione di detriti superficiali. Questi tendono ad ossidarsi e divenire più duri del materiale superficiale, creando una sorta di polvere abrasiva responsabile di una usura continua. Nel caso di materiali ferrosi, la polvere assume un colore marrone, mentre con ossidi di magnesio e alluminio il colore tende al nero.
La resistenza al fretting
La resistenza al fretting varia notevolmente a seconda dei materiali. Le leghe a base di cobalto per indurimento superficiale sono tra le migliori. In generale, acciaio su acciaio e ghisa su ghisa sono buone combinazioni, ancora meglio ottone su acciaio. Invece, accoppiando ghisa con alluminio, magnesio, cromo, stagno o plastica si ottengono scarse resistenze a fretting. Siccome un importante problema del fretting, come detto, è la resistenza a fatica ridotta, la generazione di tensioni superficiali di compressione nel materiale è benefica. Questa si può ottenere mediante trattamento termico o lavorazione a freddo ed è effettivamente utile per ritardare la propagazione delle cricche da fatica indotte da fretting. I lubrificanti a bassa viscosità tendono a ridurre l’intensità del fretting, probabilmente grazie al fatto di proteggere l’interfaccia attiva dall’ossigeno e ritardando l’ossidazione delle particelle.
Per eliminare il fretting, paradossalmente, può essere sufficiente aumentare la pressione fra le superfici a contatto, in modo da arrestarne il movimento relativo. Tuttavia, se il movimento relativo dovesse continuare, la maggiore pressione causerebbe al contrario un’accelerazione del danneggiamento.
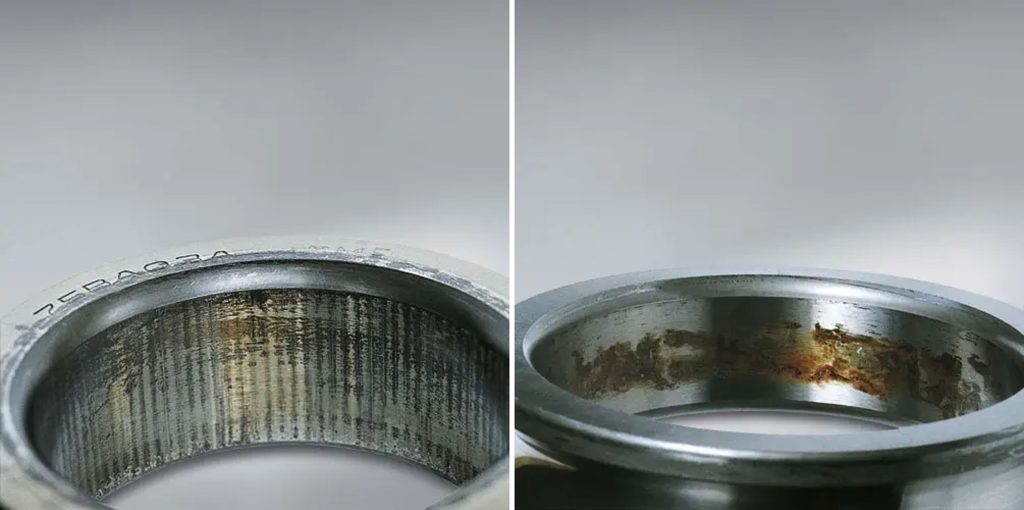
Modelli analitici dell’usura
Velocità di usura e volume asportato
La velocità di usura w si può esprimere con la cosiddetta “equazione dell’usura” come
(1)
in cui δ è la profondità di usura (mm), t il tempo (s), K il coefficiente di usura (adimensionale), H la durezza superficiale (MPa), p è la pressione superficiale di interfaccia (MPa) e v la velocità di scorrimento (mm/s).
L’equazione dell’usura implica che la velocità di deterioramento di una superficie è direttamente proporzionale al coefficiente di usura del materiale, inversamente proporzionale alla sua durezza e, assumendo un coefficiente di attrito costante, direttamente proporzionale al lavoro di attrito.
Inoltre, per una data forza di compressione totale tra le superfici, il volume di materiale asportato è indipendente dall’area di contatto. Pertanto, un’altra forma più comunemente utilizzata dell’equazione di usura è la seguente:
(2)
in cui V è il volume di materiale asportato (mm3), F la forza di compressione agente tra le due superfici (N) e S la distanza di scorrimento totale (mm).
Il coefficiente di usura
Il modo migliore per ottenere i valori del coefficiente di usura per una particolare applicazione progettuale è attraverso dati sperimentali per la stessa combinazione di materiali, i quali possono essere analizzati in condizioni sostanzialmente identiche a quelle di servizio. Inoltre, in letteratura tecnica sono disponibili molti valori di K per le più diffuse combinazioni di materiali, sempre misurati in test di laboratorio. Quando si utilizzano questi valori, è importante che la temperatura delle superfici, le tipologie di materiali e le caratteristiche della lubrificazione siano corrispondenti a quelle utilizzate nei test di laboratorio.
Per molte applicazioni, i coefficienti di usura variano da 10-1 a 10-8. I dati sperimentali dei coefficienti di usura presentano una notevole dispersione, per cui è bene considerare una variazione possibile di più o meno quattro volte dal valore riportato. Per esempio, se il coefficiente di usura riportato è pari a 1⋅10-3, il valore effettivo di varierà da 0.25⋅10-3 a 4⋅10-3. Questa variabilità è correlata a quella del coefficiente di attrito dei materiali (a cui il valore di K è legato). In Figura 4 si riportano alcuni valori del coefficiente di usura per diversi materiali, lubrificazione e modalità di usura.
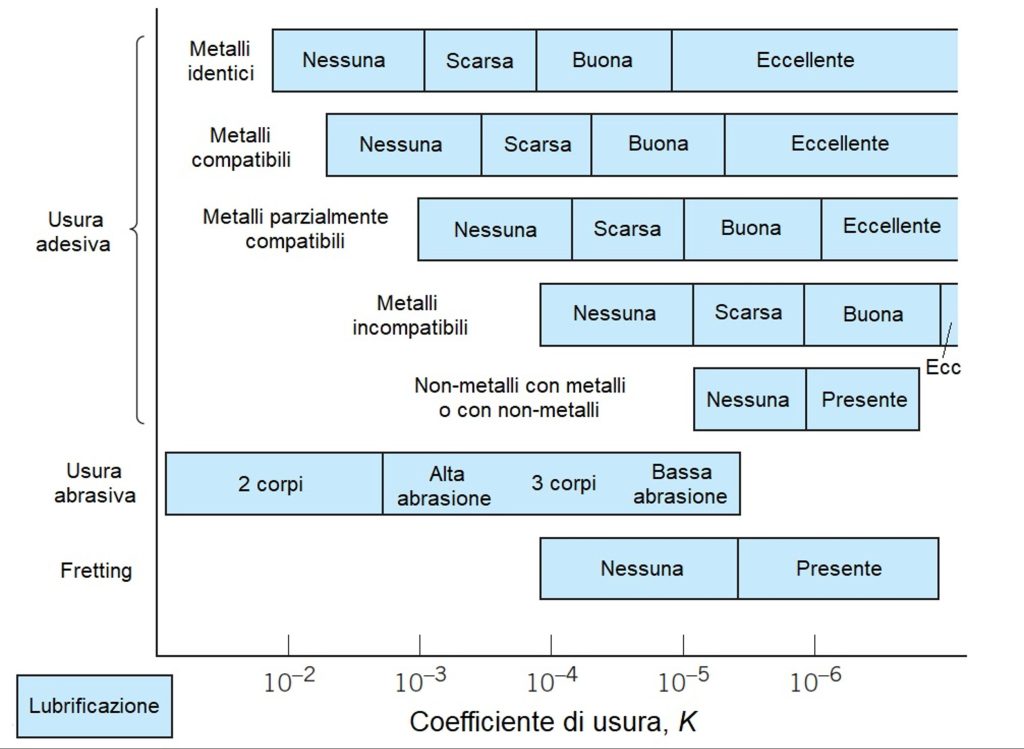
Misura sperimentale del coefficiente di usura
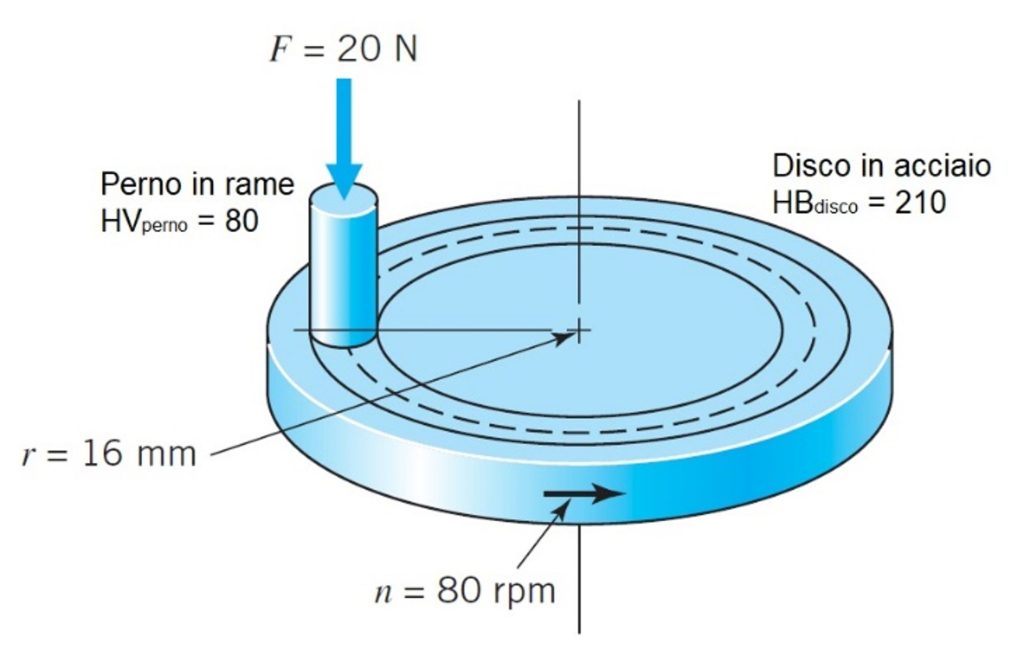
Un metodo di prova adatto alla misura diretta del coefficiente di usura è il test “pin-on-disk” (Figura 5), il quale prevede di premere un perno con estremità arrotondata non lubrificata contro un disco rotante. In questo esempio [2] si considera un perno in rame (durezza Vickers ) premuto con forza pari a 20 N su un disco in acciaio (durezza Brinell ). Il contatto strisciante avviene al raggio , con velocità di rotazione del disco . Il test si conclude dopo un tempo , quando perno e disco vengono pesati. La pesatura rivela che l’usura adesiva ha causato perdite di peso equivalenti a volumi di usura Vperno = 2.7 mm3 per il perno in rame e Vdisco = 0.65 mm3 per il disco in acciaio.
La distanza di strisciamento complessiva si può calcolare come

Le durezze in Vickers e Brinell devono essere convertite in MPa nel modo seguente:
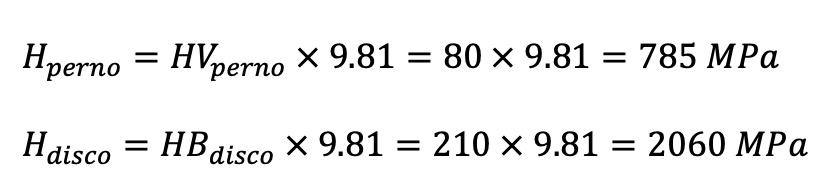
Applicando la Eq.(2) si ricavano i coefficienti di usura:
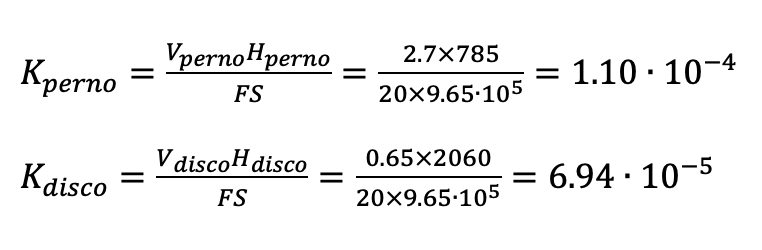
Come ci si poteva attendere, il coefficiente di usura minore si ricava per il disco in acciaio.
Lubrificazione
Abbiamo visto le caratteristiche del fenomeno dell’usura, che si innesca in presenza di superfici a contatto e in moto relativo. Con il termine di lubrificante si intende qualsiasi sostanza interposta fra le superfici che riduce l’attrito e l’usura. I lubrificanti sono solitamente liquidi ma possono essere solidi, come la grafite, il PTFE o il bisolfuro di molibdeno, oppure anche gassosi, come l’aria compressa.
I lubrificanti liquidi, sostanzialmente rappresentati da oli a differente viscosità e composizione, possiedono proprietà differenti fra loro e importanti da selezionare correttamente per le varie applicazioni. I loro nomi contengono indicazioni su queste proprietà, oltre all’indicazione degli eventuali additivi a differente funzione. Gli additivi possono servire a mantenere una bassa viscosità dell’olio anche a basse temperature o comunque a ridurre le variazioni di viscosità con la temperatura. Questa caratteristica è fondamentale per esempio nel caso dell’avviamento di un motore a freddo e con temperatura ambientale bassa, in cui si deve garantire da subito una adeguata lubrificazione. Altri additivi servono ad evitare la formazione di bolle d’aria in condizioni di moto turbolento, oppure per svolgere una funzione antiossidante e prevenire la corrosione delle superfici metalliche. Alti ancora servono a minimizzare la formazione di depositi grazie a una funzione detergente e disperdente.
I grassi sono lubrificanti liquidi, addensati per fornire proprietà altrimenti non disponibili nel lubrificante liquido tradizionale. I grassi vengono solitamente utilizzati laddove è necessario che il lubrificante rimanga in posizione, in particolare quando la lubrificazione frequente risulta difficile o costosa. Spesso, rimanendo in posizione per fornire lubrificazione, il grasso serve anche a prevenire l’ingresso di contaminanti dannosi tra le superfici a contatto. A differenza degli oli, i grassi non possono circolare e quindi svolgere una funzione di raffreddamento e pulizia. A parte questo, i grassi sono in grado di svolgere tutte le funzioni dei lubrificanti fluidi.