I principali meccanismi di cedimento degli alberi sono dovuti a corrosione, usura, sovraccarico statico e fatica. I primi due, corrosione e usura, raramente determinano il cedimento dell’albero della macchina e, nelle rare occasioni in cui lo fanno, lasciano evidenze chiare. Degli altri due meccanismi, la fatica è più frequente rispetto al sovraccarico statico. I cedimenti da sovraccarico sono causati da tensioni che superano la tensione limite del materiale, la quale assume un valore specifico a seconda che il materiale dell’albero sia duttile o fragile. Generalmente, gli alberi impiegati nella progettazione di macchine sono acciai al carbonio basso o medio legati e relativamente duttili. Di conseguenza, quando su questi materiali viene applicato un sovraccarico estremo, essi subiscono una deformazione plastica prima di giungere a rottura.
di Giorgio De Pasquale ed Elena Perotti
La progettazione a fatica
La fatica è stata identificata molto tempo fa dalla comunità scientifica. Uno dei primi test di fatica documentati risale al 1829 ad opera di tale W. Albert. Il cedimento per fatica avviene a causa della comparsa (superficiale) e della propagazione (in profondità) di microfratturazioni, o cricche, nel materiale. Questo danneggiamento risulta essere progressivo, irreversibile, indotto dall’applicazione di carichi variabili anche di entità nettamente inferiore alla tensione limite statica. Quindi, il cedimento per fatica è dovuto alla formazione e propagazione di cricche. È possibile che azioni di corrosione agiscano in concomitanza con il carico di fatica e accelerino il cedimento dell’albero.
Altro aspetto decisivo è il fatto che il danneggiamento a fatica è di natura statistica, così come la durata di vita a fatica di un particolare componente. Ciò significa che la progettazione a fatica non consente di determinare con precisione la durata di un componente (in modo appunto “deteministico”), ma piuttosto di calcolare la probabilità con cui si prevede un guasto, sulla base di una grande popolazione di campioni.
L’innesco delle cricche di fatica si localizzano solitamente sulla superficie del componente, in presenza preferibilmente di un difetto (microscopico o macroscopico) oppure di un punto di intensificazione delle tensioni, come la discontinuità rappresentata dalla cava di una chiavetta, una scanalatura, uno spigolo non raccordato, una filettatura (laddove nasce il cosiddetto “effetto di intaglio”). Un esempio di cedimento per fatica è rappresentato in Figura 1, in cui si mostra la superficie di rottura di un albero motore in AISI 4320; l’innesco del fenomeno di fatica è partito cedimento è partito dalla cava della chiavetta in alto nei punti B e si è propagato progressivamente come evidenziato dalle classiche striature parallele.
Quando la sezione dell’albero si è ridotta al punto da non essere in grado di reggere il carico statico, è avvenuto il cedimento del componente in modo plastico, nella zona C. Il fenomeno del cedimento per fatica è particolarmente insidioso poiché avviene, si è detto, a carichi molto minori dei valori di guardia per il collasso statico, e inoltre il danneggiamento avviene internamente al componente ed è pressoché invisibile a normali ispezioni visive. Gli unici modi per rilevare un danneggiamento da fatica in corso sono di tipo indiretto, ad esempio con l’uso di radiografie, liquidi penetranti o misurando la risposta in frequenza. Si tratta comunque di procedure che implicano il fermo impianto per ispezioni programmate.
Dal punto di vista della progettazione, l’approccio “safe life” consiste nel dimensionare i componenti a fatica in modo tale che un loro eventuale cedimento non possa avvenire entro la durata di servizio prevista, consentendo con la manutenzione programmata, di sostituire i componenti critici con un ragionevole anticipo rispetto all’eventualità di un danneggiamento in corso. Di contro, l’approccio di progettazione “fail safe” prevede l’impiego di più componenti in configurazione ridondante, tale per cui un eventuale cedimento di uno di essi non pregiudichi il funzionamento del sistema, proprio grazie ad un altro componente omologo che entra in funzione al suo posto.
Caratteristiche degli alberi
L’albero è un elemento rotante delle macchine, di solito di sezione circolare, che trasmette potenza o movimento da un punto ad un altro, oppure da una macchina che genera potenza verso una macchina che assorbe potenza. È uno degli elementi più comuni e fondamentali utilizzati in varie modalità negli equipaggiamenti meccanici. Gli elementi collegati all’albero producono sollecitazioni diverse, riconducibili a carichi di tipo flessionale, assiale e torsionale. L’albero deve essere sufficientemente resistente per sopportare queste sollecitazioni, sia in campo statico sia dinamico, laddove possono intervenire effetti di amplificazione dovuti a vibrazioni o risonanze. Allo stesso modo, l’albero deve resistere al cedimento per fatica, pertanto il processo di progettazione coinvolge varie fasi e spesso alcune iterazioni tra una fase e l’altra. Le principali sono queste:
- Analisi dei requisiti di potenza e coppia
- Analisi delle specifiche degli elementi accoppiati all’albero (ad esempio, il rapporto di trasmissione di ruote dentate)
- Definizione della geometria e del layout dell’albero
- Studio delle sollecitazioni
- Selezione del materiale
- Dimensionamento statico e a fatica e definizione delle dimensioni preliminari
- Analisi della deformazione flessionale e torsionale (rigidezze dell’albero)
- Studio del comportamento dinamico, analisi delle vibrazioni e determinazione delle velocità critiche di risonanza
- Selezione degli elementi collegati da catalogo (cuscinetti, chiavette, anelli elastici, etc.)
- Controllo finale, analisi delle tolleranze, prescrizione delle lavorazioni, eventuale simulazione con software specifici (analisi agli elementi finiti, FEA).
Metodi di progettazione a fatica
I metodi di progettazione a fatica prevedono il calcolo della durata del componente in numero di cicli (N), fino al cedimento in presenza di un certo livello di carico. I tre principali modelli di stima della durata di vita a fatica utilizzati nella progettazione meccanica sono il metodo “stress-life”, il metodo “strain-life” e il metodo della frattura lineare elastica. Per la progettazione degli alberi si adotta il primo, di cui analizziamo le caratteristiche.
L’American Society for Testing and Materials (ASTM) definisce la “resistenza a fatica” (σf) come il valore di stress al quale si verifica il cedimento dopo N cicli di carico; definisce inoltre il “limite di fatica” (σD) come il valore limite di stress al quale il cedimento si verifica soltanto con N molto grande, oppure al quale il cedimento non si verifica affatto. Possiamo intendere quindi che esista un limite al valore di tensione al di sotto del quale il componente manifesta vita infinita a fatica; tale limite è proprio il limite di fatica.
Sfortunatamente tale limite non risulta identificabile per tutti i materiali, e nemmeno per tutti i metalli. Acciaio, leghe ferrose e leghe di titanio hanno un valore definito del limite di fatica, che convenzionalmente viene identificato per durate almeno pari a N = 106 cicli. Altri metalli non ferrosi strutturali come alluminio e rame non presentano un limite di fatica definito, il che significa che il cedimento a fatica avverrà comunque, anche per carichi molto bassi e per numero di cicli molto alto. Il numero di cicli a rottura per fatica (N) è funzione di vari fattori, come si osserva da evidenze sperimentali, fra cui:
- il valore di tensione medio e alternato,
- il tipo di materiale,
- il trattamento termico e le condizioni superficiali del materiale,
- il profilo di durezza del materiale,
- la presenza di impurità nel materiale,
- il tipo di carico applicato (trazione, compressione, flessione, etc.),
- la temperatura di esercizio,
- la presenza di agenti corrosivi.
Prove di fatica
La resistenza alla fatica di un componente di una macchina può essere determinata, seppur attraverso una procedura lunga, mediante test di fatica in laboratorio. Ci sono diversi tipologie, fra le più comuni, di prove di fatica che si distinguono in prove ad alta e bassa frequenza, in prove a controllo di carico e a controllo di spostamento. I test ad alta frequenza tendono ad essere abbinati a carichi ridotti, in regime elastico mentre i test a bassa frequenza generalmente coinvolgono deformazioni plastiche.
Le prove di fatica prescritte dalle normative si riferiscono a condizioni di prova standard, che comprendono l’uso di campioni predefiniti in forma, dimensioni e geometria. Attraverso queste prove standard e questi provini standard è possibile ricavare le curve carico-durata (le cosiddette curve S-N) relative alla resistenza a fatica di un dato materiale. Le stesse curve S-N che si possono reperire su manuali e libri di testo catalogate per materiale, sono ottenute mediante le stesse prove normate. È quindi corretto considerare queste curve come caratteristiche della durata a fatica del materiale, non del componente.
Infatti, quando si considera uno specifico componente, caratterizzato da una geometria specifica e relativi gradienti di tensione, con particolari modalità di applicazione del carico e, magari, trattamenti specifici di natura tecnologica del materiale, la resistenza a fatica può essere anche molto diversa da quella misurata sul provino standard.
Esistono modelli che consentono di “trasferire” le proprietà di resistenza a fatica di un materiale alle corrispondenti proprietà di un componente realizzato con lo stesso materiale; questi modelli considerano specialmente fattori peggiorativi come la rugosità superficiale, l’effetto del tipo di carico agente sul componente, l’effetto della scalatura dimensionale e gli effetti di intagli che intensificano localmente la tensione. Si tratta di modelli che estendono il carico monoassiale tipico delle prove standard di fatica a condizioni di carico multiassiale esistenti nel componente reale. Sebbene questi modelli (Sines, Crossland, e altri) siano un valido strumento per una prima stima della durata a fatica del componente, è sempre consigliabile corroborarli con prove sperimentali eseguire direttamente sul componente stesso.
Tornando ai provini standard delle prove normate, per la stima della resistenza a fatica, questi vengono sottoposti a carichi ripetuti di ampiezza specifica (nel caso delle prove a controllo di carico) fino alla rottura, contando il numero di cicli. Le prove possono avvenire imponendo flessioni ripetute (prova a flessione alterna) oppure mettendo in rotazione il provino con carico fisso (prova a flessione rotante) oppure con assetti diversi, sempre secondo normativa.
Dopo aver eseguito un certo numero di prove per contemplare la natura statistica del fenomeno della fatica, è possibile identificare il grafico S-N di resistenza a fatica o diagramma di Wöhler. In questi grafici, solitamente rappresentati in scala doppio logaritmica, si riporta la curva di resistenza limite per diversi livelli di ampiezza di carico, con valore medio nullo. La sollecitazione utilizzata è quindi di tipo “alterno simmetrico”, ovvero tale da applicare una sollecitazione di trazione e una di compressione per metà periodo ciascuna, come riportato in Figura 2.

I parametri del ciclo di carico sono:
Rapporto di tensione
Rapporto di ampiezza
con σmax = tensione massima, σmin = tensione minima, σm = tensione media, σa = ampiezza di tensione.
Un esempio di diagramma S-N è riportato in Figura 3, sia a livello qualitativo (a) sia sperimentale (b). Esistono grandi quantità di dati disponibili in letteratura relativamente ai diagrammi S-N, con grafici associati a pacchetti software per vari materiali. Come già detto, non è realistico pensare che il limite di resistenza a fatica di un componente strutturale ingegneristico corrisponda ai valori misurati in laboratorio su provini standard e ulteriori analisi sono comunque raccomandabili.
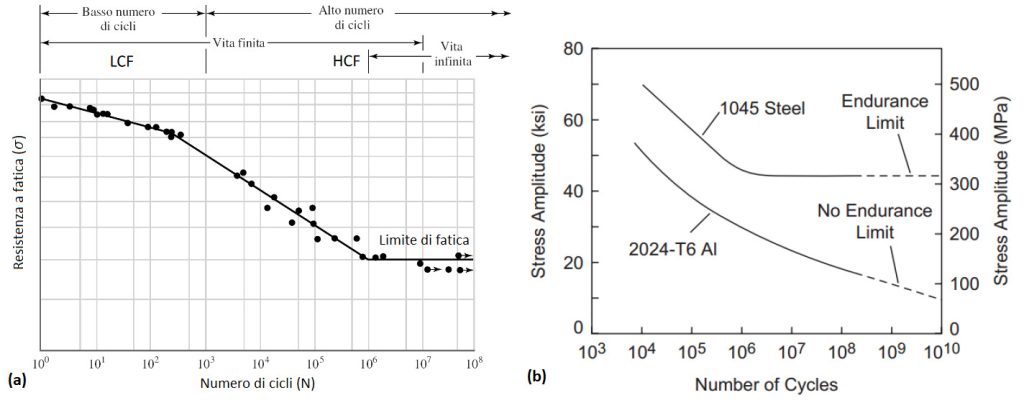
La curva di Wöhler può essere identificata da un’equazione semplificata, valida nell’intervallo di durata fra 103 e 106 cicli, così definita:
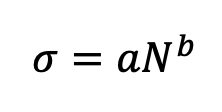
in cui i coefficienti a, b si calcolano come
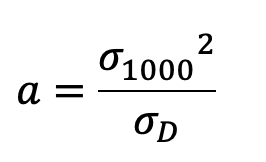
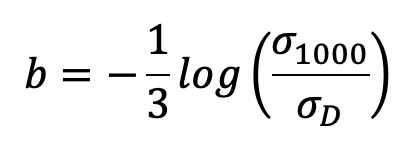
e in cui σ1000 è la resistenza a fatica a N = 1000 cicli.
Effetto di intaglio
La geometria di un albero è generalmente assimilabile a quella di un cilindro con diametro variabile. Queste variazioni di diametro sono necessarie per realizzare spallamenti che consentono il montaggio di componenti come ingranaggi, cuscinetti, pulegge e altri per vincolarne lo spostamento assiale. Queste variazioni locali di geometria, così come altre elementi quali scanalature, gole di scarico, fori e cave agiscono come zone di intensificazione (o amplificazione) della tensione e quindi come potenziali punti critici per la fatica (Figura 4). In prossimità di questi elementi dell’albero lo stato di tensione risulta alterato a livello locale e si osserva un innalzamento dell’intensità della sollecitazione e la comparsa di componenti di sforzo multiassiali.
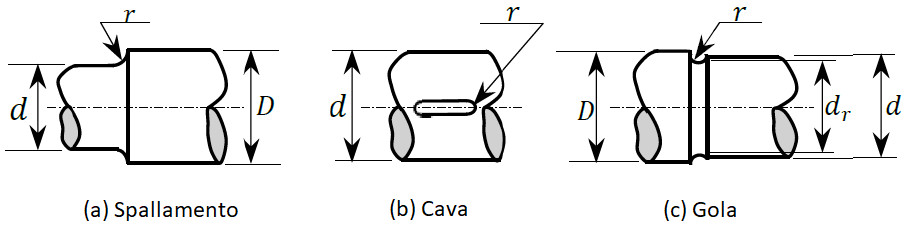
Un opportuno coefficiente, definito fattore di concentrazione delle tensioni in campo ciclico (kf) viene utilizzato per amplificare la tensione nominale in presenza di intagli. Questo fattore si calcola a partire dal fattore di intensificazione delle tensioni in campo statico (kt), che è disponibile in appositi grafici in base alla geometria dell’intaglio, al tipo di carico e alle dimensioni caratteristiche dell’intaglio stesso. Si possono usare le seguenti relazioni:
fattore di concentrazione delle tensioni in campo ciclico
sensibilità all’intaglio secondo la formula di Neuber
in cui ρ è una caratteristica del materiale e r è il raggio di gola dell’intaglio. La sensibilità all’intaglio q può assumere valori variabili fra 0 (sensibilità nulla, kf=1) e 1 (sensibilità massima, kf=kt). Il valore della sensibilità all’intaglio può anche essere ricavata da grafici sperimentali come quelli di Figura 5.
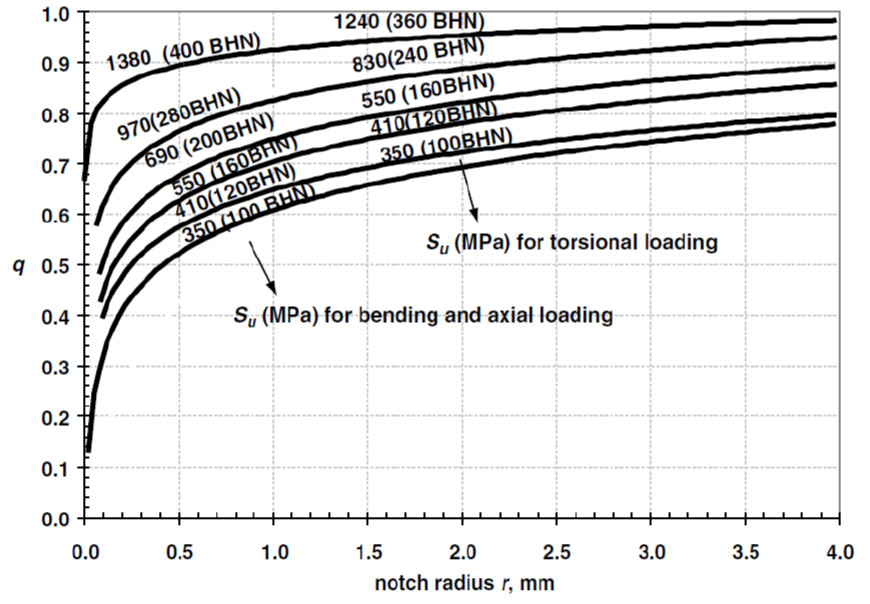
Materiali
La selezione di un materiale per una parte di macchina o un componente strutturale è una delle decisioni più importanti che il progettista è chiamato a prendere. La selezione effettiva di un materiale per una particolare applicazione può essere semplice oppure molto controversa. Per alberi e assali di trasmissione di potenza si utilizzano comunemente barre di acciaio al carbonio lavorate (AISI/SAE 1020-1050) o leghe (AISI/SAE 4140, 4145, 4150, 4340 e 8620) trafilate a freddo oppure rullati a caldo.
Tipicamente, le barre in acciaio trafilate a freddo vengono utilizzate per alberi di dimensioni piccole, inferiori a 70 mm, mentre gli acciai rullati a caldo sono comunemente utilizzati per dimensioni più grandi. La trafilatura a freddo migliora non solo la resistenza meccanica ma anche la lavorabilità, la finitura superficiale e l’accuratezza dimensionale. Gli alberi rullati a caldo sono spesso temprati e rinvenuti per una maggiore resistenza e successivamente rifiniti (torniti e levigatura e in seguito rettifica) per una migliore finitura e precisione dimensionale. Quando è richiesta una maggiore resistenza, come per applicazioni ad alta velocità, si utilizzano acciai legati con nichel, nichel-cromo o acciai al cromo-vanadio. Quando si desidera resistenza alla corrosione, vengono utilizzate alcune leghe di rame. La Tabella 1 elenca i materiali in acciaio al carbonio semplice comunemente utilizzati per la progettazione degli alberi e le loro proprietà meccaniche.
Tabella 1. Acciai tipicamente utilizzati per la fabbricazione di alberi per la trasmissione di potenza.
Materiale (AISI) | Lavorazione: Rullatura a caldo (RC) Trafilatura a freddo (TF) | Tensione di rottura (MPa) | Tensione di snervamento (MPa) |
1020 | RC TF | 380 470 | 210 390 |
1030 | RC TF | 470 520 | 260 440 |
1035 | RC TF | 500 550 | 270 460 |
1040 | RC TF | 520 590 | 290 490 |
1045 | RC TF | 570 630 | 310 530 |
1050 | RC TF | 620 690 | 340 580 |
Fattore di sicurezza
Il fattore di sicurezza (FS, S) è un coefficiente utilizzato per amplificare il valore del carico massimo atteso in una data applicazione a causa della impossibilità di determinare con certezza tutti gli effetti che possono presentarsi in modo imprevisto. A livello pratico, esso descrive la capacità di resistere a un carico oltre al valore atteso di progetto. Molti componenti sono realizzati appositamente in modo molto più resistente rispetto a quanto necessario per un utilizzo normale proprio per fronteggiare in sicurezza situazioni di emergenza, carichi imprevisti, uso scorretto o deterioramento.
Come scegliere i fattori di sicurezza
La scelta del valore del coefficiente di sicurezza da utilizzare per una particolare applicazione è una delle fasi più importanti e delicate della progettazione. La difficoltà della scelta risiede nel dover valutare le molteplici incertezze associate ai modelli usati per la progettazione nominale. Spesso occorre adottare una scelta di compromesso fra resistenza maggiorata, peso, costo, e altri fattori. Alcuni fattori da considerare nella scelta del fattore di sicurezza sono il grado di incertezza con cui sono noti i carichi esterni, le condizioni dell’ambiente di lavoro, la accuratezza e ripetibilità delle misure delle proprietà del materiale, le approssimazioni del metodo di calcolo.
Nella pratica, il progettista deve cercare di considerare la variabilità di tutti i fattori che influenzano i risultati della progettazione. Se il fattore di sicurezza è troppo basso, la possibilità di cedimento indesiderato può diventare troppo elevata, ma se il fattore è eccessivamente grande, il progetto risulta inutilmente sovradimensionato, antieconomico e non funzionale. Ad esempio, valori molto elevati possono avere un effetto inaccettabile sul peso di un velivolo. I valori del coefficiente variano tipicamente da 1.3 a 6, a seconda della confidenza dei vari fattori in gioco e della criticità dell’applicazione, ovvero dal livello di rischio associato a un possibile cedimento.
A meno di circostanze speciali, l’uso di valori del coefficiente di sicurezza a fatica inferiori a 1.5 non è accettabile. Un livello di compromesso che non mette a rischio la sicurezza è pari a 3 per quanto riguarda la progettazione a fatica. Il progettista deve fare affidamento in primo luogo alle normative eventualmente esistenti per l’ambito di progetto, in subordine a banche dati storiche a livello aziendale o di settore, e in caso di innovazioni senza particolari precedenti è raccomandata una scelta cautelativa possibilmente supportata da evidenze sperimentali su prototipi.
Criteri generali
In generale, i seguenti accorgimenti dovrebbero essere seguiti durante la progettazione di alberi per evitare cedimenti per fatica.
Il calcolo teorico deve comprendere un adeguato fattore di sicurezza, specialmente dove si verificano concentrazioni di stress (ad esempio, chiavette, intagli e cambi di sezione) e dove le incertezze sui dati di progetto e sul modello utilizzato sono più ampie.
Adottare ampi raggi di raccordo nei cambi di sezione e in presenza di altri intagli dell’albero, legati a motivi funzionali.
Scegliere materiali, se possibile, che possiedono una tensione limite di fatica, come ad esempio la maggior parte degli acciai, e fare in modo che i livelli di sollecitazione rimangano al di sotto di tale limite.
Prevedere opportune lavorazioni e trattamenti superficiali. Esempi efficaci sono la pallinatura, la nitrurazione e altri trattamenti che inducono stati di compressione superficiale. Sono invece da evitare quei trattamenti che al contrario determinato uno stato di tensione residua di trazione, come ad esempio l’elettroplaccatura.
Specificare finiture superficiali di qualità per gli operatori addetti alle lavorazioni.
Evitare condizioni di lavoro in ambienti corrosivi.
Quando possibile, eseguire misure sperimentali dello stato di tensione, specialmente per le saldature soggette a carichi ciclici e potenzialmente a cedimento per fatica.
Riferimenti
S.K. Armah, Preliminary Design of a Power Transmission Shaft under Fatigue Loading Using ASME Code, American Journal of Engineering and Applied Sciences, 2018.
R.G. Budynas, J.K. Nisbett, 2016. Shigley’s mechanical engineering design. Mechan. Eng.